Fiber optic gyroscope industry market
With its unique advantages, fiber optic gyroscope has a broad development prospect in the field of precision physical quantity measurement. Therefore, exploring the influence of optical devices and physical environment on the performance of fiber optic gyros and suppressing the relative intensity noise have become the key technologies to realize the high precision fiber optic gyro. With the deepening of research, the integrated fiber gyroscope with high precision and miniaturization will be greatly developed and applied.
Fiber optic gyroscope is one of the mainstream devices in the field of inertia technology at present. With the improvement of technical level, the application scale of fiber optic gyro will continue to expand. As the core component of fiber optic gyros, the market demand will also grow. At present, China's high-end optical fiber ring still needs to be imported, and under the general trend of domestic substitution, the core competitiveness of China's optical fiber ring enterprises and independent research and development capabilities still need to be further enhanced.
At present, the optical fiber ring is mainly used in the military field, but with the expansion of the application of optical fiber gyroscope to the civilian field, the application proportion of optical fiber ring in the civilian field will be further improved.
According to the "2022-2027 China Fiber Optic Gyroscope industry Market Survey and Investment Advice Analysis Report" :
The fiber optic gyroscope is a sensitive element based on the optical fiber coil, and the light emitted by the laser diode propagates along the optical fiber in two directions. The difference of light propagation path determines the angular displacement of the sensitive element. Modern fiber optic gyro is an instrument that can accurately determine the orientation of moving objects. It is an inertial navigation instrument widely used in modern aviation, navigation, aerospace and national defense industries. Its development is of great strategic significance to a country's industry, national defense and other high-tech development.
Fiber optic gyro is a new all-solid-state fiber optic sensor based on Sagnac effect. Fiber optic gyro can be divided into interferometric fiber optic gyros (I-FOG), resonant fiber optic gyro (R-FOG) and stimulated Brillouin scattering fiber optic gyro (B-FOG) according to its working mode. According to its accuracy, fiber optic gyro can be divided into: low-end tactical level, high-end tactical level, navigation level and precision level. Fiber optic gyroscopes can be divided into military and civilian according to their openness. At present, most fiber optic gyros are used in military aspects: fighter and missile attitude, tank navigation, submarine heading measurement, infantry fighting vehicles and other fields. Civil use is mainly automobile and aircraft navigation, bridge surveying, oil drilling and other fields.
Depending on the accuracy of the fiber optic gyroscope, its applications range from strategic weapons and equipment to commercial grade civilian fields. Medium and high-precision fiber optic gyroscopes are mainly used in high-end weapons and equipment fields such as aerospace, while low-cost, low-precision fiber optic gyroscopes are mainly used in oil exploration, agricultural aircraft attitude control, robots and many other civilian fields with low precision requirements. With the development of advanced microelectronics and optoelectronics technologies, such as photoelectric integration and the development of special fiber optics for fiber optic gyros, the miniaturization and low-cost of fiber optic gyros have been accelerated.
Summary
Ericco's fiber optic gyro is mainly a medium precision tactical fiber optic gyro, compared with other manufacturers, low cost, long service life, the price is very dominant, and the application field is also very wide, including two very hot selling ER-FOG-851, ER-FOG-910, you can click the details page for more technical data,
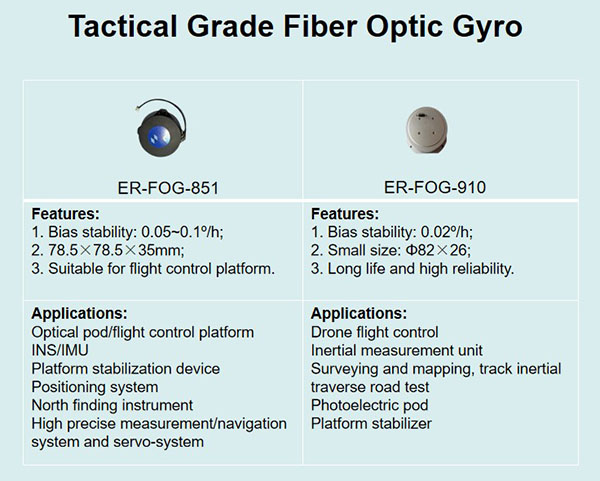
If you have any purchase needs, feel free to send the inquiry, or contact us directly: Phone: +86-13992884879
Email: info@ericcointernational.com.