For the full article, click here https://www.ericcointernational.com/application/influence-of-ambient-temperature-on-measurement-data-of-tilt-sensor.html
1. How to reduce the impact of ambient temperature on the tilt sensor?
At present, the tilt sensor is widely used to measure the inclination Angle of various structures, such as foundation pit, slope, dam, railway system, etc., which can reflect the stability and safety of the structure. Temperature will affect the inclinometer sensor, which is the cause of the fluctuation of the measurement data of the inclinometer sensor. At present, the influence of ambient temperature on the measurement of the tilt sensor can be reduced by improving the hardware of the inclination sensor, such as changing the temperature of the heat source inside the sensor, adding the temperature compensation circuit, etc., but this method is more expensive and less accurate than the method that considers the relationship between the measurement data and the change of ambient temperature to establish the temperature compensation formula. Moreover, most of the measurements of inclination sensors are tested in the laboratory, and the sensor with temperature compensation function is redesigned according to the measurement results in the laboratory, which is different from the application of inclination sensors in practical engineering. Therefore, we analyze the inclination sensor data measured in the actual engineering environment, and establish the temperature compensation formula with appropriate fitting method, so as to reduce the influence of ambient temperature on the inclination sensor measurement data.
2. Principle of influence of temperature on measurement data of inclination sensor
We set up an inclinometer sensor on a slope that needs to be monitored and use an automated monitoring platform to collect and receive sensor data in real time. We analyzed the original data of the inclination sensors extracted from July 15 to August 15, 2022, and the analytic results of part of the inclination sensors are shown in Figure 1.
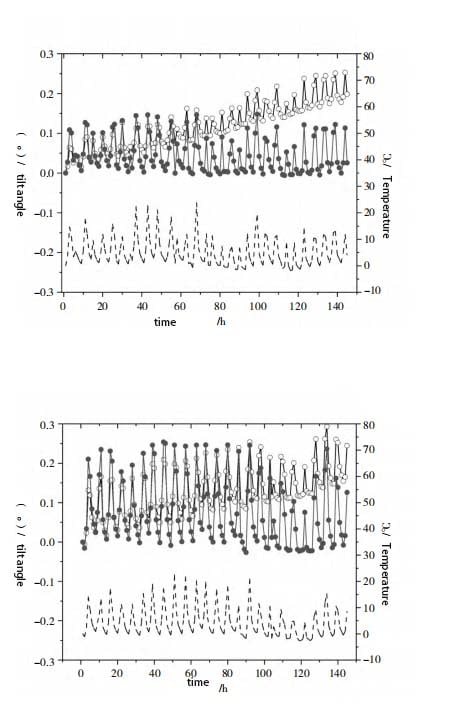
As can be seen from Figure 1, the inclination of Angle X and Angle Y of the inclinometer sensor is significantly affected by temperature. The higher the ambient temperature is, the greater the data inclination Angle is. Moreover, Angle X is significantly affected by temperature than Angle Y, indicating that the ambient temperature has a greater impact on the output of the signal of the inclination sensor. The inclination sensor has a large temperature fluctuation error due to the change of ambient temperature in practical application. This is because under the influence of temperature, there will be some changes in the parameters of the devices in the sensor, which will affect the measurement accuracy and reliability of the sensor. Therefore, it is necessary to consider the influence of ambient temperature on the data, and establish the temperature compensation formula according to the actual measurement data of the inclination sensor, so as to correct the measurement data of the inclination sensor.
3. Establishment of temperature compensation formula
First, the influence range of temperature should be determined. As can be seen from Figure 1, the X Angle of inclinometer sensors 01 and 02 basically has no deviation during the period from July 15, 2022 to August 15, 2022. The data measured by inclination sensors 03 and 04 are analyzed. Moreover, the relative offset of X Angle of each sensor is less than ±0.025° (indicating that the floating error caused by temperature is small). The results are shown in Table 1.
Tilt sensor | Temperature range |
01 | 26~31 |
02 | 26~30 |
03 | 26~33 |
04 | 26~30 |
As can be seen from the statistical data in Table 1, when the inclination sensor is at (28±2) ℃, it can be seen from Figure 1 that the inclination degree of the inclination sensor X Angle and Y Angle is significantly affected by temperature. The higher the ambient temperature is, the greater the data inclination Angle is, and the influence of temperature on X Angle is more obvious than that of Y Angle. It shows that the ambient temperature has a great influence on the output of the inclinometer sensor signal, and the inclination sensor has a great temperature fluctuation error in practical application due to the change of ambient temperature. This is because under the influence of temperature, there will be some changes in the parameters of the devices in the sensor, which will affect the measurement accuracy and reliability of the sensor. Therefore, it is necessary to consider the influence of ambient temperature on the data, and establish the temperature compensation formula according to the actual measurement data of the inclination sensor, so as to correct the measurement data of the inclinometer sensor.
Moreover, it can be seen from Figure 1 that there is a linear relationship between the influence of temperature on the output value of the inclination sensor signal, and the following linear temperature compensation formula can be established:
X1=X0-A×(T-28) (1)
Y1=Y0-A×(T-28) (2)
Where: X0 is the original output value of X Angle of the inclination sensor, (°); Y0 is the original output value of the Angle Y of the inclination sensor, (°); X1 is the tilt Angle of the corrected X Angle, (°); Y1 is the tilt Angle of the corrected Y Angle, (°); T is the ambient temperature value output by the inclinometer
sensor, (°); A is the temperature compensation coefficient; A×(T-28) is a ring
Output increment due to ambient temperature. The size of the temperature compensation coefficient A is constantly adjusted to obtain better compensation effect, and the proportional coefficient of the temperature compensation coefficient A of each inclination sensor is finally obtained, as shown in Table 2.
Tilt sensor | The scale coefficient of A |
X Angle | Y Angle |
01 | 0.007 | 0.004 |
02 | 0.013 | 0.008 |
03 | 0.005 | 0.004 |
04 | 0.010 | 0.004 |
4. Analysis of temperature compensation effect
The results of X Angle and Y Angle corrected by the temperature compensation formula are shown in Figure 2. As can be seen from FIG. 2, the fluctuation of X Angle and Y Angle under the influence of temperature change after being corrected by the temperature compensation formula becomes significantly smaller. The variance of X Angle data of tilt sensor 01 is 0.001 950, and the modified variance is 0.000 169. The X-angle data variance of tilt sensor 02 is 0.00 648, and the corrected variance is 0.000 493. It can be seen from the above that the X and Y angles corrected by the temperature compensation formula are affected by the temperature change, and the fluctuations generated are reduced by one order of magnitude, indicating that equations (1) and (2) can effectively weaken the influence of ambient temperature on the measurement of the inclination sensor, improve the measurement accuracy of the inclination sensor, and meet the measurement needs of the actual environment.
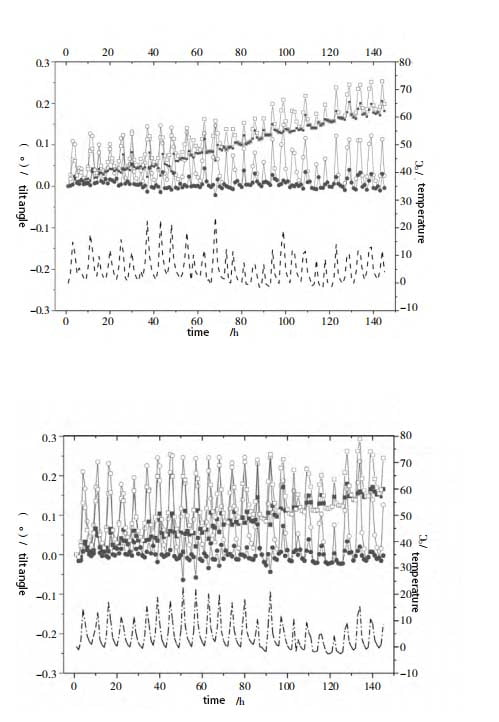
From the temperature difference of 1.5 ° C, 20 different grades of temperature are selected in the operating temperature range of the inclination sensor -20 ~ 70 ° C for testing. According to the annual temperature difference of about 30 ° C in Guangdong Province, the inclination sensor is put into the temperature control box. Starting from 5 ° C, the temperature difference interval of 1.5 ° C is heated. Keep heating up to 35 ° C and observe the data change. 7 different levels of pressure are selected from the range of -15° ~ 15° of the inclination sensor. Considering the basic level of the initial Angle when the inclination sensor is installed, the maximum installation inclination Angle does not exceed 10°, the cumulative variation given by the design unit of the project does not exceed 60 mm, and the maximum height of the slope is 10 m. According to the trigonometric function, the Angle is 0.35°, so the maximum Angle of the test is 12°. Then a test is performed every 4° from -12° to 12°, and the X and Y directions are involved in the test, with a total of 280 data. MATLAB software is selected to realize the verification and analysis of the model. The accuracy of the maximum relative error is verified by the formula as follows:

The results show that when the inclination is 10.5° and the temperature difference is 30 °, the error reaches 0.3°. After compensation, the maximum error is better than 0.01°; The maximum error before compensation is 12% and the maximum error after compensation is 0.15%. The compensation effect is good.
5 Summary
We study the influence of temperature on the measurement accuracy of the inclination sensor, and find that the inclination sensor has a large temperature fluctuation error due to the change of ambient temperature in practical application. In order to reduce the influence of the ambient temperature on the measurement accuracy of the inclination sensor, the temperature compensation formula is established based on the actual measurement data of the inclination sensor, and the relationship between the measurement data and the ambient temperature is fully considered. The main conclusions are as follows:
(1) The ambient temperature has a significant effect on the inclination sensor, and the higher the temperature, the greater the measurement error. Moreover, the temperature compensation coefficients of each inclination sensor are different, indicating that different inclination sensors are affected by temperature to different degrees.
(2) The error of X Angle and Y Angle measured by the inclination sensor is different under the influence of temperature, and the error of X Angle under the influence of temperature is larger than that of Y Angle. For example, ER-TS-12200-Modbus is a dual-axis monitoring system. In actual measurement, the error is different due to the influence of temperature. The error of X Angle due to the influence of temperature is larger than that of Y Angle.
(3) Considering the relationship between the measurement data and the change of ambient temperature, the temperature compensation formula is established and applied. The results show that the proposed temperature compensation formula can effectively reduce the influence of ambient temperature on the measurement accuracy of the inclination sensor.
Although it is greatly affected by the ambient temperature, such as our ER-TS-32600-Modbus and ER-TS-4250VO, temperature compensation formulas can be established to effectively correct and apply their measurement data, so as to reduce the impact of ambient temperature on the measurement accuracy of the sensor.