Ericcogyro is a leader supplier of Inertial Sensor products North Finder,North seeking system,DTG,FOG,MEMS Gyroscope,Accelerometer,IMU,INS,electronic compass, our inertial sensor are sold worldwide and get the good feedback from our clients .
Sunday, May 21, 2023
Wednesday, May 17, 2023
Friday, May 12, 2023
Exploring Tilt Sensor Precision: Accuracy in Motion Detection
Tilt sensors are electronic devices that measure the orientation or inclination of an object relative to the Earth's gravitational field. They find extensive use in various industries, including automotive, aerospace, robotics, and construction. This article aims to delve into the concept of tilt sensor precision, highlighting its importance, factors influencing accuracy, and applications where precise tilt measurements are crucial.
Tilt sensor precision refers to the ability of a tilt sensor to provide accurate and reliable measurements of angular displacement. It is a critical parameter in applications where precise tilt detection is essential for maintaining safety, efficiency, and optimal performance. The level of precision required depends on the specific application and the tolerances within which the system operates.
Several factors contribute to tilt sensor precision. One key aspect is the sensor's resolution, which determines the smallest detectable change in tilt that the sensor can measure. Sensors with higher resolution offer finer increments of measurement, resulting in enhanced precision. Additionally, the accuracy of the sensor's internal components, such as accelerometers or gyroscopes, significantly affects the overall precision of the tilt measurement.
Environmental conditions also play a crucial role in tilt sensor precision. Factors such as temperature fluctuations, vibration, electromagnetic interference, and humidity can influence the accuracy of the measurements. Therefore, it is essential to consider these environmental factors and select tilt sensors that are designed to operate reliably in the intended environment.
Furthermore, the calibration process of tilt sensors greatly impacts their precision. Calibration ensures that the sensor's output corresponds accurately to the actual tilt angle. Regular calibration is necessary to maintain precision over time, as sensors may experience drift or inaccuracies due to aging or prolonged use. By calibrating the sensor periodically, its precision can be preserved and any deviations or errors can be corrected.
The applications that require precise tilt measurements are numerous. In the aerospace industry, for example, Ericco tilt sensors are used in aircraft and spacecraft to monitor the orientation of various components, such as wings, stabilizers, or solar panels. Accurate tilt measurements are crucial for maintaining the desired flight dynamics and stability of the vehicle.
In construction and civil engineering, tilt sensors play a vital role in monitoring the inclination of structures, such as buildings, bridges, or dams. Precise tilt measurements help detect any unwanted deviations from the desired alignment, enabling timely corrective actions to ensure structural integrity and safety.
Tilt sensors also find application in robotics, where precise motion control and stability are essential. By accurately measuring tilt angles, robotic systems can adjust their movements, maintain balance, and perform tasks with precision. This is particularly important in industries such as manufacturing, automation, and healthcare, where robots work alongside humans or handle delicate objects.
In conclusion, tilt sensor precision is crucial for accurate and reliable measurement of angular displacement. Factors such as resolution, sensor calibration, and environmental conditions significantly influence the precision of tilt sensors. Understanding and considering these factors is essential when selecting tilt sensors for applications where precise tilt measurements are vital. Whether in aerospace, construction, or robotics, the ability to obtain precise tilt data ensures safety, efficiency, and optimal performance in a wide range of industries.
Sunday, April 9, 2023
What are the limitations and potential drawbacks of gyro sensors, and how can consumers make informed decisions about when and how to use them?
Gyro sensors are an important component of many electronic devices, providing accurate and reliable motion sensing capabilities. However, like any technology, gyro sensors have limitations and potential drawbacks that consumers should be aware of when making decisions about when and how to use them.
Limitations
One limitation of gyro sensors is their inability to measure absolute position. Gyro sensors measure angular velocity, which can be integrated over time to determine relative orientation. However, without additional information from other sensors, such as accelerometers or GPS, gyro sensors cannot determine absolute position.
Another limitation of gyro sensors is their sensitivity to external factors such as vibration and shock. This can lead to errors in the sensor's readings, particularly in high-vibration environments. To mitigate this issue, some gyro sensors are designed with advanced vibration and shock resistance features.
A potential drawback of gyro sensors is their power consumption. Gyro sensors require a significant amount of power to operate, which can drain the battery life of devices such as smartphones and gaming controllers. To address this issue, some devices use low-power gyro sensors or implement power-saving features such as turning off gyro sensors when they are not in use.
Potential drawbacks
One potential drawback of gyro sensors is their susceptibility to drift over time. Gyro sensors can gradually shift from their initial position over time, leading to errors in the sensor's readings. This can be mitigated through regular calibration, but if left unchecked, drift can lead to significant inaccuracies in the sensor's measurements.
Another potential drawback of gyro sensors is their susceptibility to interference from magnetic fields. Magnetic fields can cause gyro sensors to produce erroneous readings, particularly in devices with weak or poorly shielded sensors. To minimize the impact of magnetic interference, gyro sensors should be shielded or placed away from other magnetic components in the device.
Informed decisions
Consumers can make informed decisions about when and how to use gyro sensors by considering the limitations and potential drawbacks of the technology. When evaluating devices that use gyro sensors, consumers should consider the accuracy and reliability of the sensors, as well as their power consumption and susceptibility to interference.
Consumers should also consider the environment in which the device will be used. Devices that will be used in high-vibration environments or near magnetic sources may require more advanced gyro sensors or additional shielding to maintain accuracy and reliability.
Finally, consumers should be aware of the importance of regular calibration and maintenance to ensure optimal performance and longevity of gyro sensors. Devices with built-in calibration tools make this process easy and convenient, but it is still important for users to take an active role in maintaining their device's sensors.
Conclusion
Ericco gyro sensors are a powerful technology that provide accurate and reliable motion sensing capabilities in many electronic devices. However, they have limitations and potential drawbacks that consumers should be aware of when making decisions about when and how to use them. By understanding the capabilities and limitations of gyro sensors and taking an active role in maintaining their devices, consumers can make informed decisions and enjoy the benefits of this technology for years to come.
Wednesday, February 22, 2023
Introduction of North Seeking MEMS IMU — ER-MIMU-01 and ER-MIMU-05
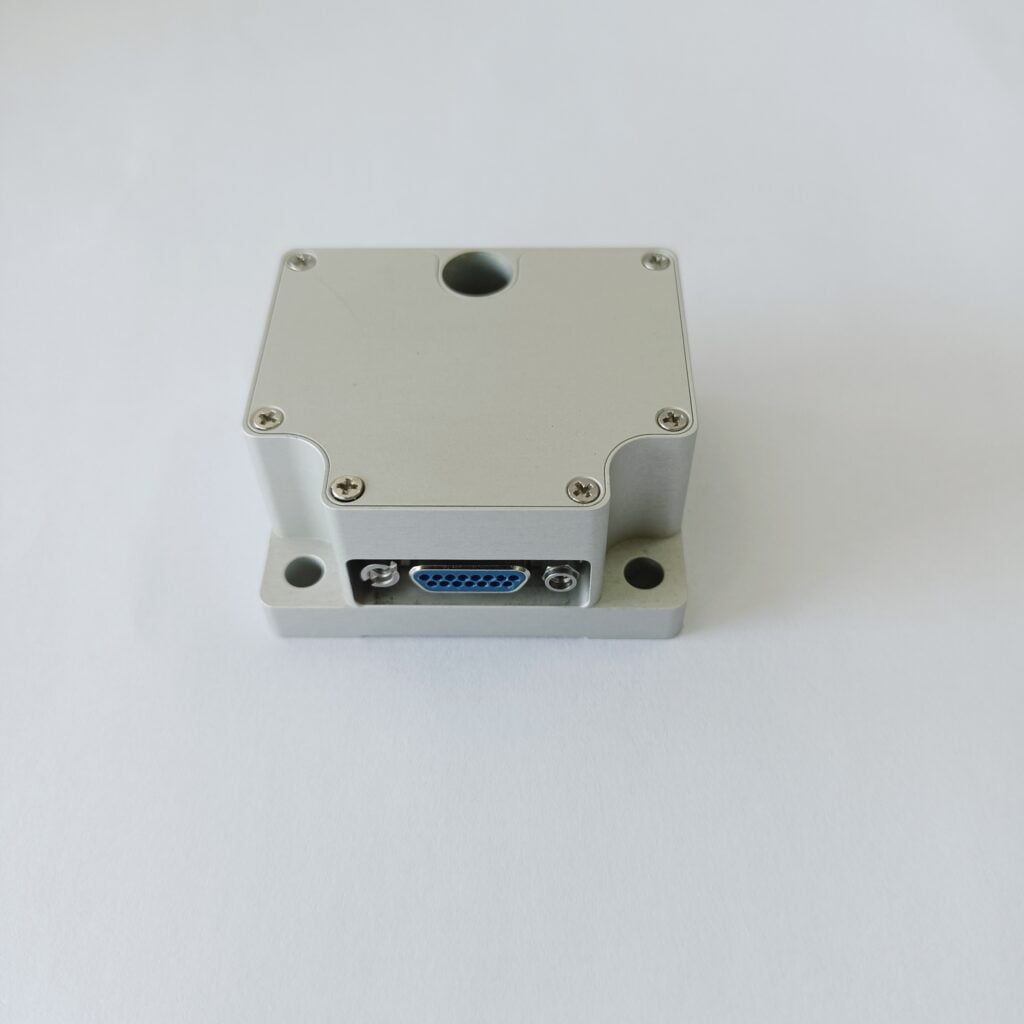
Ericco released new products MEMS North Seeking IMU, ER-MIMU-01 and ER-MIMU-05 . They have the following common features:
ER-MIMU-01 ER-MIMU-05
3-axis gyro & 3-axis accelerometer;
Measuring range 100% /s;
Gyro bias instability: 0.02/h
Gyro bias stability(10s l0)<0.1/h;
5V power supply, low power consumption of 1.0W;
Operate Temp: -45℃~+85℃;
RS422 bus communication.
They can be applied to the following fields:
Construction machinery dip angle measurement, angle control, pylon operation monitoring, medical equipment angle control, satellite antenna star search, bridge, tall building, tower, dam monitoring and rock and soil monitoring, mining, attitude/heading reference system, integrated inertial navigation.
The above information about north seeking MEMS IMU is provided by our engineers. If you want to get the quotation and more technical data, please feel free to contact us.
Wednesday, February 8, 2023
MEMS Closing The Gap Between Price And Performance
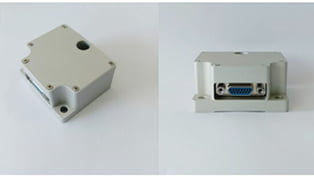
Micro-electromechanical systems (MEMS) have made rapid advances since their introduction in the 1950s. Made of tiny integrated circuits and silicon-based microelectronics, the technology has dramatically revolutionized industrial and consumer electronics alike. For inertial measurement units and inertial navigation systems, MEMS technology saw the creation of a variety of inertial sensors, including gyroscopes, accelerometers, and magnetometers.
By far, the main benefit of MEMS is its extremely low cost compared to its FOG counterparts, usually by a factor of more than 10. The use of less expensive materials, advanced manufacturing processes, smaller sizes, and mass adoption, have all contributed to MEMS being cheaper to produce. Today, it is widely used in applications ranging from in-car GPS, drones, or camera pointing, where FOG technology is simply too cost-prohibitive to make commercial sense.
MEMS devices are also very small and lightweight, allowing them to be used in tight spaces such as smartphones and toys. MEMS are now found everywhere, from consumer to industrial-grade applications in a wide range of industries. This small form factor notably fuelled the adoption of MEMS in the drone surveying market, notably LiDAR surveying, where a higher degree of accuracy is needed while remaining relatively small and lightweight in order to fit on a drone. By contrast, FOGs are considerably larger and heavier, thus reducing the number of suitable applications.
MEMS are also less power-hungry than FOGs, allowing for longer mission times for energy-constrained vehicles. Combined with their small size and lightweight properties, MEMS is the solution of choice for many unmanned vehicles that require the lowest SWaP-C (size, weight, power, and cost).
MEMS though is not without its limitations. Due to their mechanical nature and components vibrating at a high frequency, MEMS are more sensitive to vibrations, especially at harmonic frequencies. Vibrations can increase the noise of a sensor’s output signal, causing a bias that needs to be corrected via software.
This issue can have some practical consequences. A non-negligible number of drone gyroscopes have been found to have resonant frequencies in both the audible and ultrasonic frequency ranges, making them vulnerable to loudspeaker noises. Therefore, it is possible to crash a drone at distance via a “sonic attack” using speakers set at the right frequency.
MEMS are also typically prone to g-sensitivity errors in gyroscope measurements due to linear acceleration, leading to large biases directly affecting the accuracy of attitude estimation in an INS. While acceleration is often short – just a few seconds – but intense – 5g or more in highly-dynamic fields such as unmanned aerial vehicles, the accumulation of errors over time cannot be neglected, and need to be compensated for. Corrections are done at the filter level but add another degree of complexity that FOG alternatives are less susceptible to.
We are a North-Seeking MEMS IMU supplier. If you are interested in our products, please contact us now!
Sunday, January 15, 2023
Come and Buy High-Quality FOG INS
Do you know what INS is? Ericco provides FOG ins and MEMS ins solutions, which can be customized according to user needs. At present, our ER-FINS-70 low cost fog INS has been in hot sale. It is mainly composed of three solid fiber optic gyroscopes, three quartz flexible accelerometers, data packing plates, body structural parts and related software. It can measure the angular velocity and linear acceleration of the carrier motion; performs the error compensation of temperature, installation misalignment angle, non-linearity and zero position etc.; Automatically searches and outputs true north heading; provides three-dimensional attitude; provides information for carrier attitude and navigation control and the measurement result is output through RS422 serial interface. If you want to know more technical data and quotations, please feel free to contact us.
What does MEMS gyroscope tell you?
Stable Flight for Drones✈️ | Precise Control for Robots🤖 | Stable Navigation for Autonomous Driving🚗 | High-Precision Measurement for In...

-
With the advantages of all-solid state, high performance and flexible design, fiber optic gyroscope has become the mainstream inertial...
-
For more information, please indicate in the “Ask for a Quote” box at the bottom of the page that you learned about this North Finder fr...
-
Horizontal directional drilling technology completes the task of laying underground pipelines without destroying the surface environment....