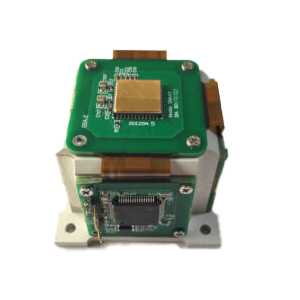
Concept
The full name of IMU is Inertial Measurement Unit. The IMU contains a 3-axis accelerometer and a 3-axis gyroscope. It is a device that measures the three-axis attitude angle (or angular velocity) and acceleration of an object. The IMU can calculate the position and attitude of the carrier by measuring the angle and acceleration of the carrier in three-dimensional space. Advances in IMU technology are revolutionizing the positioning and navigation industry, and the gap between microelectromechanical systems (MEMS) gyroscopes and fiber optic gyroscopes (FOG) is closing as new MEMS gyroscope sensors achieve greater accuracy. The two most common types of IMUs today are built around microelectromechanical systems (MEMS) technology and fiber optic gyroscope (FOG) technology.
Concept of MEMS IMU & FOG IMU
1.MEMS IMU
The MEMS IMU contains a MEMS accelerometer and a MEMS gyroscope. MEMS accelerometers detect linear acceleration, which can then be used to calculate speed and distance. MEMS gyroscopes detect rotational motion and are typically used to determine heading and/or attitude (roll and pitch). When data from accelerometers and gyroscopes are combined over time, the position of an object relative to its origin can be calculated.
Because of their small size, mainstream manufacturing processes, use of common materials, and widespread adoption, MEMS IMUs are, on average, smaller, lighter, consume less power, and are cheaper than their FOG counterparts. However, because MEMS IMUs contain more micromechanical components and are more sensitive to temperature fluctuations, they tend to be less precise and noisier than their fiber optic counterparts. If accurate position data is required over an extended period of time, MEMS IMUs are often used in conjunction with GNSS receivers or other sensor technologies that provide supplementary position information.
MEMS inertial sensors are small, lightweight, low power and low cost, in other words they have all the most desirable characteristics of low SWaP-C (size, weight, power and cost). Applications include mobile phones, vehicle navigation systems, autonomous ground vehicles, flying drones and robotic systems.
Because MEMS sensors are smaller and lighter, they are more sensitive to unmodeled temperature and vibration effects due to their mechanical properties. These effects increase noise (angular random walks) and lead to biases in the modeled noise figure. The IMU independently developed by Ericco Inertial Systems Co., Ltd. in China provides high-reliability, low-cost FOG/MEMS inertial measurement units to global customers. Ericco not only provides standard IMU products, but can also customize FOG/MEMS according to customers’ special requirements. For example, ER-MIMU-01 uses MEMS accelerometer and gyroscope with high quality and reliability, RS422 and external communication, baud rate can be flexibly set between 9600~921600, through the communication protocol to set the user’s required communication baud rate. With X, Y, Z three-axis precision gyro, X, Y, Z three-axis accelerometer with high resolution, can be output by RS422 X, Y, Z three axis of gyroscope and accelerometer’s original hexadecimal complement data (including gyro hexadecimal complement the numerical temperature, angle, the accelerometer hexadecimal temperature, the acceleration hexadecimal complement number); It can also output float dimensionless values of the gyroscope and accelerometer processed by the underlying calculation.
2.FOG IMU
As the name suggests, FOG IMU is a type of IMU that uses optical fiber to measure the angular velocity or rotation rate of any object. Due to the low noise of fiber optic gyroscopes, this technology has been widely used in demanding navigation applications. FOGs are inherently more accurate and stable than MEMS-based systems, making them an alternative in scenarios where GNSS signals are unavailable (such as mining and navigation applications) or where GNSS denial may occur. Another notable feature of FOG is its rapid north-seeking capability. The FOG IMU can measure the Earth’s angular rotation and achieve heading in just minutes, even as the IMU itself moves.
Fiber optic gyroscopes use fiber optic loops and measure the interference of light beams in opposing loops to detect rotation about each axis. The hardware used is more expensive, larger and typically consumes more power, but its lack of moving parts makes it less sensitive to temperature changes and mechanical vibrations. And FOG gyrocompasses have no moving parts, making them more resistant to vibration and shock than MEMS gyrocompasses. This means they are ideally suited for applications that may experience intense vibration levels, such as demanding high temperature, high vibration environments such as mining, defence, surface ships and aerospace, and heavy equipment stabilization.
The ER-FIMU-50 FOG IMU is the most cost-effective inertial measurement device for navigation, control and dynamic measurements. This is the smallest FOG IMU developed by Ericco (same performance as KVH 1775). The system uses high-reliability closed-loop fiber optic gyroscopes and accelerometers, and uses multiple compensation techniques to ensure measurement accuracy. Strict technology is used in the manufacturing process to ensure that the angular and linear motion parameters of the carrier can be accurately measured under harsh conditions.
The product has a good user experience. In addition to wide voltage power supply, users can also configure the output bandwidth, data update rate, communication port baud rate and communication protocol as needed. It can be used in aviation track reference systems, guidance control systems, ship attitude measurement, inertial/satellite integrated navigation systems, drilling systems, mobile surveying and mapping systems, mobile satellite communications and other fields.
Differences between MEMS IMU and FOG IMU:
Due to the different gyroscopes they have, these two types of IMUs are very different. Their 10 differences will be introduced below.
1.Technology:
MEMS IMUs use microelectromechanical systems with accelerometers and gyroscopes based on micromachining technology.The FOG IMU uses a fiber optic gyroscope, which utilizes the principle of light interference in optical fibers.
2.Working principles:
MEMS IMUs use the deflection of microstructures due to acceleration or rotation to measure motion.
The FOG IMU measures motion by detecting the phase shift of light due to rotation in a fiber optic coil.
3.Accuracy:
Compared to MEMS IMUs, FOG IMUs have higher accuracy and precision. This makes them particularly useful in situations where users rely on the IMU for long periods of time: accurate systems can calculate a position close to the true position even after hours.
4.Size and shape:
MEMS IMUs are smaller and more compact, making them suitable for integration into smaller devices such as consumer electronics.
FOG IMUs are typically larger and heavier, and are often used in larger systems such as aerospace and defense applications.
5.Cost:
MEMS IMUs are generally more cost-effective than FOG IMUs, making them widely used in consumer products.
FOG IMUs are more expensive due to their greater precision, highly specialized internal components, and complex advanced manufacturing processes.
6.Energy consumption:
MEMS IMUs typically have lower power consumption, making them suitable for portable and battery-operated devices.
FOG IMUs consume more power, which is less important in applications such as land vehicles and aircraft where power supplies are readily available.
7.Application:
MEMS IMU can be used for north seeking in logging tools/gyro tools, pointing, steering and initial alignment in guided weapons/drone launch systems in advanced mining/drilling equipment, direction in satellite antennas, target tracking systems , pointing and tracking navigation-level MEMS guidance and navigation in weapon systems, directional railway train systems, navigation-level MEMS IMU/INS for precise attitude and position, measurement of north seeking and positioning in geodesy/land mobile mapping systems, Oil exploration, bridges, high-rise buildings, towers, dam monitoring, geotechnical monitoring, mining, etc.
FOG IMUs are commonly used in aerospace, defense, marine navigation and other high-precision applications, particularly where GNSS is unavailable or unreliable, such as underground mining or military environments.
8.Robustness:
MEMS IMUs can be susceptible to environmental factors such as extreme temperatures and high vibrations, which can affect their accuracy.
The FOG IMU is more robust and stable, making it better suited for particularly harsh and demanding environments.
9.Calibration and automatic north seeking:
Due to possible drift over time, MEMS IMUs may require more frequent calibrations to maintain accuracy. They are not sensitive enough to automatically find an accurate heading unless connected to a GNSS receiver.
FOG IMUs have better long-term stability and typically require less frequent calibrations to maintain accurate heading or position. The most accurate fiber optic gyroscope systems are so sensitive that they can determine where north is by detecting the Earth’s rotation.
10.Integration:
Because MEMS IMUs are smaller and have lower power requirements, they are easier to integrate into compact devices.
FOG IMUs are typically used in larger systems to accommodate their size and weight and their higher power needs.
Selection of MEMS IMU and FOG IMU
In summary, the choice of IMU depends on the application and environment. You can choose the IMU type that suits you according to different application scenarios, accuracy requirements, etc.
MEMS IMUs are ideal for: lightweight, small size, low power consumption, short-range pointing sensors, and GNSS integration in predictable dynamic environments.
FOG IMU is suitable for: absolute attitude accuracy, high temperature, high vibration, bias stability over time.
Read the reference: https://www.ericcointernational.com/inertial-measurement-units
Contact me:
Email: info@ericcointernational.com
Whatsapp: 139 9288 4879