Ericcogyro is a leader supplier of Inertial Sensor products North Finder,North seeking system,DTG,FOG,MEMS Gyroscope,Accelerometer,IMU,INS,electronic compass, our inertial sensor are sold worldwide and get the good feedback from our clients .
Thursday, April 18, 2024
Wednesday, April 17, 2024
Why is Tilt Sensor Used?
Tilt sensors are also known as inclinometers. They are a type of position sensor used to measure the Angle or slope of an object.
Inclinometers are one of the most common types of position sensors and are widely used in many industries.
1.Tilt sensor application
Tilt sensor Angle and slope. So anything that works on Angle will use a inclinometer sensor or a rotary position sensor.
Some sample applications include:
Robotics: Tilt sensors are used to sense the Angle of the robot arm to ensure that the arm movement is in a precise position.
Marine applications: inclinometer sensors are used in a variety of Marine applications, especially boom Angle sensing.
Industrial vehicles: In industrial vehicles, tilt sensors are used to monitor tip protection and for a variety of applications in cranes and construction vehicles.
Aerospace: tilt sensors are used for aircraft orientation and applications on the red arrow.
Industrial applications: Platform leveling is a popular application in the industrial sector that uses inclinometer sensors.
Safety: Tilt sensor Monitors security camera Angle sensing and mobile safety systems.
Mobile phones: Mobile phones are integrated with a very small tilt sensor that changes the orientation of the screen depending on how the phone is held.
Measure ski slope: for safety reasons.
2.How the tilt sensor works
There are different types of inclinometer sensors, and they work slightly differently.
A simple tilt sensor works by using a metal ball that connects two pins and moves within the sensor. When the sensor is tilted, the ball moves position, which connects the circuit that turns the sensor on or off.
More sophisticated inclinometer sensors use an internal gyroscope to measure the direction of the gravitational pull to determine the orientation of the device.
Ericco's tilt sensor is actually the use of MEMS plus meter in the static state can measure the principle of angular velocity. At present, there are conventional (single-axis), dynamic (two-axis), wireless inclinometer sensors, wired and wireless have their own advantages and disadvantages. We can choose the model according to the application scenario and accuracy requirements.
The single-axis ER-TS-3160VO, with an accuracy of 0.01°, is a very popular one with a wide range of applications. Is a very good choice, wireless ER-TS-12200-Modbus, accuracy up to 0.001°, is an ultra-low power, small volume, high-performance wireless inclinometer sensors, for industrial applications users do not need power supply or real-time dynamic measurement of object attitude Angle needs. Using lithium battery power supply, based on the Internet of Things technology Bluetooth and ZigBee(optional) wireless transmission technology, all internal circuits are optimized design, using industrial MCU, three-proof PCB board, imported cables, wide temperature metal shell and other measures to improve the industrial level of the product. Good long-term stability, zero drift small, can automatically enter low-power sleep mode, get rid of the dependence on the use environment. The product has compact structure, precise design, temperature and linearity compensation function, and integrates short-circuit, instantaneous high voltage, polarity, surge and other comprehensive protection functions, easy to use. Wireless digital signal transmission mode eliminates the tedious wiring and noise interference caused by long cable transmission; Industrial design has extremely high measurement accuracy and anti-interference ability. Wireless sensor nodes can form a huge wireless network, supporting thousands of measurement points to monitor the tilt at the same time, and support professional computer software. Without on-site investigation, it can measure and record the status of the tested object in real time. The safety monitoring system is suitable for remote real-time monitoring and analysis of industrial sites, dilapidated buildings, ancient buildings, civil engineering, various tower incline deformation and other needs.
3.Tilt sensor characteristics and specifications
The tilt sensor has the following characteristics;
High reliability
High accuracy
Easy to operate
Not using much electricity
Low cost
Small size, light weight, low power consumption
Anti-vibration, anti-impact, waterproof and dustproof
High stability, low noise, strong anti-interference ability
Different types of inclinometer sensors have different specifications to suit different applications. When choosing a tilt sensor, it is important to consider the following factors;
Sensitivity Some tilt sensors are more sensitive than others, depending on how the increment you need to measure affects the sensitivity of the desired sensor.
Axis number: The number of axes affects the Angle and direction that the sensor can measure.
Resolution: The resolution affects the minimum tilt that the sensor needs to detect.
Measuring range: What is the measuring Angle in the application? This will affect the type of sensor selected.
Accuracy: Different applications may require different degrees of accuracy, so it is important to choose a inclinometer sensors that reflects the requirements.
Noise tolerance: Our inclinometer sensors provide standard noise tolerance.
Certification: requires that we provide inclinometer sensors for intrinsically safe environments as well as underwater applications.
Optimization method of attitude information of shipborne inertial measurement unit
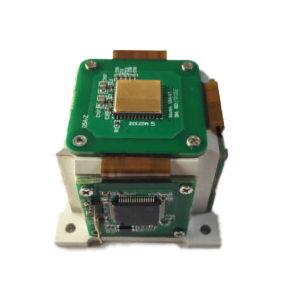
The advancement of my country's geostationary satellite technology has made satellite communication resources more and more abundant and diverse. The development of the Internet has also made big data and the Internet of Things widely used. The ocean communication network that cannot be realized by the ground wired base station communication mode must be realized through satellite communication. Therefore, the demand for shipboard communication equipment to be instantly accessible has also been greatly released. The inertial measurement unit based on the microelectronic system is the core component of the shipborne communication-in-motion antenna system and is the key to ensuring stable tracking of communication-in-motion equipment. Generally, the inertial measurement unit uses the Kalman filter method to fuse the three-axis measured angular velocity and the three-axis measured acceleration information to obtain relatively accurate dynamic attitude information of the market. However, in the actual dynamic use process, only the market information obtained through this method is The effect of applying to ship roll isolation is not ideal. It is proved by mechanism analysis and large amounts of data collection. This is due to the measurement information deviation caused by the three-axis measurement acceleration being contaminated by other accelerations when the measurement unit moves in space. In order to facilitate the distinction, This type of acceleration that affects attitude measurement is collectively called harmful acceleration. This article will analyze the causes of harmful acceleration and its impact on measuring carrier attitude Euler angle information, and propose a filtering method for harmful acceleration, which further improves the accuracy of microelectronic sensors in measuring carrier attitude information. This filtering method can be expanded to be applied to a variety of devices with interference information, especially providing convenience for the promotion and application of mobile communication series products and similar devices.
1. Kalman filter method
In order to understand how harmful acceleration affects the attitude measurement information of the inertial measurement unit, we must first understand the basic algorithm of the attitude measurement of the inertial measurement unit, namely the Kalman filter method. The principle of the Kalman filter method is to obtain the original measurement data in a probabilistic sense through multi-channel sensor measurement when the noise status of each measurement plan is known in advance. In order to cooperate with the application of Kalman filtering method, it is necessary to construct other carrier attitude measurement channels different from the direct measurement channel. Angular velocity meters and accelerometers are respectively installed on the three sign vectors of the inertial measurement unit: The actual measured attitude obtains low-noise, high-precision attitude information in a probabilistic sense, thereby obtaining accurate filtering results. The Kalman filtering process can be divided into 5 steps:
(1)The attitude estimation is set at time T, that is, when there is no carrier attitude measurement information, the attitude information estimation is obtained by the state equation operation of the attitude rotation quaternion:
(2)One-step prediction error variance matrix:
(3)Filter gain matrix:
(4)State matrix estimation:
(5)Estimated error variance matrix:
After the above five steps, the carrier attitude information expressed in the form of quaternions processed by the Kalman filter method can be accurately obtained, and then the rotation matrix and attitude Euler angle information can be obtained.
2.Harmful acceleration analysis
The inertial measurement unit (conventional strapdown inertial navigation) based on the measurement principle of three-axis angular velocity and three-axis acceleration uses the Kalman filter method to fuse the rotating eccentric attitude integral matrix with the measured gravity acceleration vector scalar data to obtain high maneuverability dynamic posture information. Since the attitude information is based on the gravity acceleration vector scalar information of the three-axis acceleration measurement, the accuracy and stability of the gravity acceleration of the three-axis acceleration measurement are an important basis for the accuracy and stability of the attitude information of the inertial measurement unit. But in actual use. The spatial motion of the inertial measurement unit is not a rational rotation of the center of mass. In the earth's inertial system, changes in the magnitude and direction of its spatial motion speed will also produce acceleration. Therefore, in addition to the acceleration due to gravity, triaxial acceleration will also measure other accelerations due to changes in space motion. The participation of these accelerations will interfere with attitude convergence and affect the accuracy of attitude information. During the attitude convergence calculation process, they are collectively called harmful accelerations.
During the use of shipboard mobile communication, the inertial measurement unit must participate in space motion. As long as the form of motion changes, there will be harmful acceleration mixed in the measured gravity acceleration data to interfere with the attitude convergence calculation. For the convenience of analysis, harmful acceleration is now divided into two categories according to its mode of action. One type of harmful acceleration is relatively stationary relative to the geodetic system, such as the linear motion acceleration of the carrier in space. This type of acceleration is relatively stationary in space with the acceleration of gravity, and its effect does not affect the attitude change of the inertial measurement unit. Therefore, the measurement information of the three-axis angular velocity and the three-axis acceleration cannot be separated, that is, it is objectively uncontrollable. Fortunately, this kind of harmful acceleration occurs instantaneously during the actual use of the shipboard communication system and its value is not large. Its interference can be reduced through appropriate Kalman filter coefficients. Another type of harmful acceleration is relatively stationary relative to the measurement coefficient of the inertial measurement unit, such as normal acceleration and tangential acceleration during ship rolling. This kind of acceleration continues to periodically interfere with the measurement data during the ship rolling process, affects the Kalman filter convergence process, and is an important factor affecting the dynamic data of the inertial measurement unit. In order to improve system performance and reduce costs, such harmful acceleration needs to be measured from three-axis acceleration
It can be seen that when the rotation radius of the instantaneous measurement system is known, the harmful acceleration can be separated from the measurement information of the three-axis acceleration through the three-dimensional angular velocity information, so as to achieve the purpose of filtering out such harmful acceleration.
However, in practical applications, the rotation radius of the roll and pitch measurement systems is related to the installation height of the ship's moving centerline and the hull draft, and the rotation radius of the yaw angle is related to the motion radius. Therefore, the rotation radius of the measurement system is not applicable. Obtained intuitively, in order to filter out such harmful acceleration, mathematical statistics must be calculated.
Summarize
The attitude information optimization method of the shipborne inertial measurement unit filters out the interference acceleration from the three-axis acceleration measurement information of the inertial measurement unit through numerical analysis, making the measured three-axis acceleration closer to the real local gravity acceleration, improving the inertial measurement unit The authenticity of the feedback information reduces the deviation between the measured attitude Euler angle and the real attitude information, thereby improving the spatial pointing accuracy of the shipborne satellite communication antenna in motion, increasing the environmental adaptability of the shipborne satellite communication system, and achieving the expected control Effect. Due to the complexity of the working environment of shipborne communication systems in the ocean and the uncertainty of interference, more testing research on inertial measurement units is needed to expand the applicable scope of inertial measurement units. ERICCO's independently developed inertial measurement units such as ER-MIMU-01 are suitable for more complex environments. The built-in gyroscope has high accuracy and can provide good positioning and orientation during work. If you want to know more, please contact our relevant technical personnel.
Tuesday, April 16, 2024
What is an Inertial Measurement Unit?
An inertial Measurement Unit (IMU) is a device that typically consists of a gyroscope for measuring angular rate and an accelerometer for measuring linear speed. In this article, we'll delve into the inner workings of an inertial measurement unit to explore all the relevant specifications and information you need to choose the right IMU for your application.
1. What is IMU?
An Inertial Measurement Unit (IMU) is a device that can measure and report the specific gravity and angular rate of an object to which it is attached. Imus typically include:
Gyro: provides angular rate measurement
Accelerometer: Provides specific force/acceleration measurement
Magnetometer (optional) : Measures the magnetic field around the system
Adding magnetometers and filtering algorithms to determine directional information results in a device called the Attitude and Heading Reference System (AHRS).
Imus are available in a variety of performance levels. According to the specifications of accelerometers and gyroscopes, they are divided into one of four categories:
Consumer/Automotive grade
Industrial grade
Tactical level
Marine class
These performance categories are often defined in terms of the sensor's operational bias stability, which plays such an important role in determining inertial navigation performance. The following table summarizes the various levels of performance for these specifications.
Class | Cost | gyroscope operation bias stability | GNSS reject navigation time | applications |
Consumer | < $10 | -- | -- | Smartphone |
Industrial grade | 100$- 1000$ | <10°/h | <1 minute | UAV |
Tactical level | $5,000- $50,000 | <1°/h | <10 minutes | smart ammunition |
Navigation class | < $100,000 | <0.1°/h | a few hours | military |
Let's dive into the specific sensors used in IMUs, namely accelerometers and gyroscopes.
2. Accelerometers
Accelerometers are the primary sensors responsible for measuring changes in inertial acceleration or velocity over time, and there are many different types, including mechanical accelerometers, quartz accelerometers, and MEMS accelerometers. MEMS accelerometers are essentially mass blocks suspended by springs, as shown in Figure 2. This mass block is called the test mass, and the direction in which the mass block is allowed to move is called the sensitivity axis. When the accelerometer is subjected to linear acceleration along the sensitivity axis, the acceleration causes the mass block to move sideways, and the amount of deflection is proportional to the acceleration.
3. Gyroscope
A gyroscope is an inertial sensor that measures the angular rate of an object with respect to an inertial reference frame. There are many different types of gyroscopes on the market with varying levels of performance, including mechanical gyroscopes, fiber optic gyroscopes (FOG), ring laser gyroscopes (RLG), and quartz /MEMS gyroscopes. Quartz and MEMS gyroscopes are typically used in the consumer, industrial, and tactical markets, while fiber optic gyroscopes cover all four performance categories. Ring laser gyroscopes typically have in-operation bias stability and range from 1°/ hour to less than 0.001°/ hour, covering tactical and navigation levels. Mechanical gyroscopes are the highest performing gyroscopes on the market with bias stability of less than 0.0001°/ hour in operation.
4. Magnetometer
A magnetometer is a sensor that measures the strength and direction of a magnetic field. While there are many different types of magnetometers, most MEMS magnetometers rely on magnetoresistance to measure the surrounding magnetic field. Magnetoresistive magnetometers are composed of permalloy, and their resistance changes in response to changes in the magnetic field. Typically, MEMS magnetometers are used to measure a local magnetic field that is a combination of the Earth's magnetic field and any magnetic fields generated by nearby objects.
5. How does the Inertial Measurement Unit (IMU) work?
A single inertial sensor can only sense measurements along or around a single axis. To provide a three-dimensional solution, three separate inertial sensors must be mounted together to form an orthogonal cluster called a triplet. This set of inertial sensors installed in a triplet is often referred to as a triaxial inertial sensor because the sensor can provide a measurement along each of the three axes. Similarly, an inertial system consisting of a 3-axis accelerometer and a 3-axis gyroscope is called a 6-axis system because it provides two different measurements along each of the three axes for a total of six measurements.
The Inertial Measurement Unit (IMU) measures and reports the raw or filtered angular rate and specific force/acceleration experience of the object to which it is attached.
The data output of the IMU is typically body frame acceleration, angular rate, and (optionally) magnetic field measurements.
The user is then responsible for determining the pose by implementing an independent fusion algorithm, such as a Kalman filter.
6 Summary
Ericco's FOG Inertial Measurement Unit ER-FIMU-50, gyro bias stability is 0.5°-1°/h, ER-FIMU-60, gyro bias stability is 0.1°-0.5°/h, these two belong to the tactical class of fiber optic IMU. ER-FIMU-70 gyro bias stability is 0.05°-0.1°/h, it belongs to the navigation level of fiber optic inertial measurement unit, mainly used in the inertial navigation of surface-to-air missiles, air-to-air missiles and navigation missiles, space stability system, mapping system, attitude reference system and other fields.
Research on inertial measurement unit output delay and time synchronization measurement method
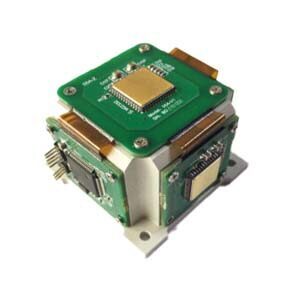
As an important feedback link in the control system, the inertial measurement unit's delay characteristics of its gyroscope channel and accelerometer channel are an important technical indicator. In actual attitude control and navigation solution systems, the output delay of the inertial measurement unit is required to be as small as possible. The better the real-time performance, the easier it is for the control system to make timely and accurate attitude corrections. Then studying the measurement method of output delay is the key to accurately evaluate the dynamic performance of inertial measurement equipment. At present, conventional delay measurement only examines the output delay of the gyro channel, and does not involve the time asynchronous problem between the acceleration channel and the angular velocity channel. In order to make up for this shortcoming, this paper proposes an angular vibration test based on the sinusoidal swing motion of the angular vibration table. On the basis of the process, the synchronous acquisition of three accelerometer channel signals is added, the raw data of the gyroscope and accelerometer are converted into the frequency domain, and then the characteristic frequency points are extracted. Finally, the time delay is calculated from the phase angle of the characteristic frequency point and the time synchronization of the inertial device is achieved of calibration.
1.Delay analysis
The output delay of the inertial measurement unit is mainly affected by the superposition of its own structural transmission , the response of the gyroscope and meter-added inertial device, digital filtering, data transmission and other links.
Structural transmission: In order to ensure a good working environment for the inertial instrument, rubber shock absorbers are usually elastically installed between the inertial instrument and the measured carrier. The response delay for the angular velocity and linear velocity transmission in the low frequency band is negligible, but for high-frequency excitation There is a certain delay in response.
The response of the inertial device itself: Due to the influence of the structure and the sensitivity of the electronic devices, the gyroscope and the meter-added inertial device themselves have a certain delay when they are sensitive to external excitation.
Digital filtering: The digital signal processing of the gyroscope itself will cause delays to the entire system during the step height filtering and output signal filtering stages, reducing the ability of the inertial instrument to track external inputs, and there is some inherent delay. After the inertial measurement unit collects instrument data, it needs to undergo low-pass filtering to remove signal noise. If the filter order is high, the phase group delay generated will affect the system response time. Taking the 50th-order FIR low-pass filter as an example, from the amplitude-frequency phase-frequency curve of the digital filter in Figure 1, we can find that: 2kHz sampling data, the phase delay generated by the excitation below 200Hz in the phase-frequency curve is linear, then the group The delay is a fixed constant value of about 12.5ms.
2.Time synchronization analysis
Research on traditional strap down inertial navigation system algorithms is based on ideal measurements from gyroscopes and accelerometers. However, in an actual IMU, the signal output of each inertial device may be asynchronous in time. The output time of the gyroscope may be later than the output time of the accelerometer, or it may be faster than the output time of the accelerometer. This is because the physical limitations of the sensor inside the inertial measurement unit will affect the conversion of the bandwidth signal, ultimately resulting in the time of the output parameter. Delay. The frequency band width of fiber optic gyroscopes is generally several thousand Hz, which is much higher than the frequency bandwidth of accelerometers, and will eventually be processed to a unified output frequency. This processing process may also cause desynchronization of the actual output signal. In addition, the filter before the AD converter may also cause additional delays in the gyroscope and accelerometer signals, which are determined by factors such as the time it takes the sampled information to be transmitted to the computer. In addition, the inertial device also needs to be processed by some auxiliary hardware to make the inertial device output a more accurate signal. Therefore, it is necessary to compensate for the sum of all physical delays of the accelerometer and gyroscope and additional software and hardware delays, that is, to test the time delay parameters through SINS. The calibration results in the process are partially compensated to synchronize the accelerometer and gyroscope outputs.
3.Measurement method
In order to fully measure the time asynchronous parameters between the three accelerometers, the time asynchronous parameters between the three gyroscopes, and the asynchronous time error between the inertial device and the standard output, the analog signal output by the closed-loop angular vibration table is used as the standard output time reference. The product under test is fixed at a certain distance from the center of the off-angle vibration table table through the vibration tooling (as shown in Figure 2). The digital signal output by the inertial measurement unit and the analog signal output by the closed-loop angular vibration table are collected by the signal receiving system and stored in the computer.
The angular vibration test is performed at a given maximum rotation angular rate of 10º/s to ensure that the input value at each frequency point remains consistent.
In the test, if the angular vibration table has an angular rate setting input, the maximum angular rate is set to 10º/s. If the angular shaking table is an amplitude setting input, the swing amplitude for each frequency needs to be calculated. The following numerical relationships exist between the two input methods. In the angular vibration test, the instantaneous rotation angle of the turntable is:
Then the instantaneous angular velocity of the turntable is:
When the maximum angular rate of the turntable rotation is known, it can be obtained from the turntable formula:
The angular vibration frequency and amplitude requirements obtained by the above formula are as shown in Table 1
Figure 2 Installation diagram
The gyro is sensitive to the sinusoidal rocking motion of the shaking table; due to the offset of the installation position, the meter has a lever arm effect, which produces centripetal acceleration during the swing process. The meter data in three directions will also reflect the characteristic frequency of the shaking table. The Fourier transform is used to respectively extract the analog signal (reference voltage) output from the closed loop of the angular shaking table and the swing frequency component in the actual output of the inertial measurement unit. Finally, the time delay is calculated and the calibration of the time synchronization of the inertial device is achieved.
Table 1 Angular vibration test frequency and amplitude relationship
4 Angular vibration test
4.1 Test process
The angular vibration test uses a pure strapdown optical fiber inertial group to conduct the test according to the installation method in Figure 2. During the test process, when the data frame sent by the inertial measurement unit is sent to the receiving acquisition system, the analog signal of the AD sampling angular vibration table of the receiving acquisition system is simultaneously triggered ( Reference voltage), and then send the inertial measurement data and reference voltage data package to the host computer test software. After the test is completed, the spectrum of the saved test data is analyzed to calculate the response delay of the inertial measurement unit and the asynchronous time between the inertial devices.
4.2 Test results
During the test, the angular vibration table was set up to swing at a frequency of 2Hz. The data output frequency of the inertial measurement unit was 2000Hz. The data were normalized to facilitate waveform comparison with the reference voltage. Perform FFT processing on the saved data of the meter channel and gyro channel to extract the characteristic frequencies, and compare the phase differences at the characteristic frequencies.
Figure 3 Characteristic frequency
Figure 4 Data Curve
Summarize
The above article describes the output delay and time synchronization measurement method of the inertial measurement unit, and conducts an angular vibration test on it. The test results show that the waveforms between the three gyroscopes of the inertial measurement unit (and between the three plus meters) are basically consistent. The asynchronous time between similar devices is not greater than 0.1ms, which is much smaller than the data sampling time and does not require compensation. The MEMS IMU independently developed by ERICCO is divided into navigation grade and tactical grade. For example, navigation grade ER-MIMU-01 and tactical and ER-MIMU-03 have relatively high accuracy. If you want to know more, please contact us.
Monday, April 15, 2024
What can Fiber Optic Gyroscopes be Used for?
1.What is a fiber optic gyroscope?
A fiber optic gyroscope (FOG) is a device used to measure angular velocity and direction. It provides extremely accurate rotational speed information with low maintenance costs and long service life.
Fiber optic gyroscopes are becoming more affordable, and the technology has proven beneficial for an ever-expanding array of different high-performance inertial navigation systems (INS). As a result, FOG has become the default choice for strategic and tactical level applications that require long-term navigation in environments where GNSS (Global Navigation Satellite System) is not available.
2.How does a fiber optic gyroscope work?
Fiber optic gyroscopes use the properties of light in closed circuits to estimate changes in direction. Two beams of light are sent in opposite directions in the fiber coil.
As the vehicle rotates, the beam traveling against the rotation experiences a slightly shorter path delay than the other beams, a phenomenon known as the Sagnac effect. The phase shift difference between the two beams is then used to estimate the rotation rate.
3.What is the difference between a ring laser gyroscope and a fiber optic gyroscope?
Similar to the FOG, the ring Laser gyroscope (RLG) is an optical gyroscope that utilizes the Sagnac effect. The main difference between the two is the way they are constructed, because a ring laser gyroscope uses a laser passing through a system of mirrors to determine the rotation of the vehicle, rather than a simple fiber optic coil.
In addition to requiring extremely high manufacturing precision and special mirrors, the RLG is also filled with gas, and the laser needs to be "dithered," or mechanically vibrated, to prevent laser locking to eliminate small rotations.
While both types of gyroscopes work similarly and are very accurate, the older toroidal laser gyroscope technology is more sophisticated due to its construction, requires more maintenance, and is generally more expensive. In contrast, the fiber optic gyroscope is a solid-state device that does not use a jitter mechanism, which means it does not produce any acoustic vibrations, making it more durable and reliable than the RLG. In addition, the application of fiber optic gyroscopes can be extended by changing the length and diameter of the fiber optic coils.
4.What is the difference between a fiber optic gyroscope and a MEMS gyroscope?
A MEMS (Micro-electro-mechanical System) gyroscope is a smaller, lighter gyroscope made from tiny devices. MEMS gyroscopes have significantly reduced SWaP-C, which means they are preferred for applications requiring small payloads.
FOG has higher inertial performance and lower deviation, making it the preferred solution for high-precision applications such as GNSS rejection environments or antenna pointing.
5.What can fiber optic gyroscopes be used for?
Fiber optic gyroscope technology facilitates a growing number of applications where accurate heading and navigation are critical. This includes both manned and driverless vehicles.
Surface Ocean Vehicles: Ocean survey vessels use fiber optic gyroscopes to determine pitch, roll, and heading in real time and build accurate position data for unmanned underwater vehicles (UUV). They are particularly useful for side-scan sonar and similar applications.
Undersea vessels: Manned vehicles (such as submarines) and UUVs (unmanned underwater vehicles), including autonomous underwater vehicles (AUVs) and remotely operated vehicles (ROVs), rely on fiber-optic gyroscopes for precise navigation in extremely challenging and dangerous environments at minimal cost. Or an unreliable source of absolute location. Rovs and AUVs for hydrology in particular benefit from FOG's precision.
Aviation: Helicopters can be subject to electromagnetic interference and can benefit greatly from FOG-based INS. Unmanned aerial vehicles (UAVs) and commercial aircraft typically require FOG-level performance to reduce the risk of losing GNSS locations while in flight. The accuracy of roll, pitch and yaw data is critical to the safe operation of the aircraft.
Defense: Ground-based defense vehicles must not rely on GPS/GNSS because of the risk of local interference or spoofing of these signals, or simply the risk of terrain blocking or altering satellite positioning data. Fibre-based INS allows these vehicles to operate seamlessly, preventing adversaries from gaining an advantage from these tactics.
Space exploration: Fiber optic gyroscopes are ideal for space applications due to their long service life, virtually maintenance-free, extremely low power consumption, and accurate navigation data.
Robotics: Directional data from the fiber optic gyroscope is used to navigate the robot, ensuring safe operation when adjusting for any changes in speed, position or acceleration.
Ericco's ER-FOG-50, ER-FOG-60 small size, light weight, the use of digital closed loop mode, no wear parts, long service life, a wide range of applications, is our good choice, if you are interested in our products, please feel free to contact us.
Who Makes Fiber Optic Gyroscopes?
1.The use of gyroscopic technology
For more than 100 years, gyroscopic technology has been used to aid navigation in a variety of applications. Mechanical gyroscopes were relied upon for about 60 years until the invention of the ring laser gyroscope in the 1960s. However, it wasn't until the 1970s that fiber optic gyroscopes were developed, implemented, and became popular in a wide range of applications from submarines to spacecraft.
The goal of any gyroscope is to measure the angular rotation rate on any single axis. This is critical for determining the pitch, roll, and yaw angles in a system that requires reliable navigation information to function properly. Imagine a plane taking off, a NASA rocket diving, or a missile finding its target. Gyroscopes for such applications measure the angular rotation rate of each vehicle. This critical information is sent downstream to control and stabilize the vehicle. Each gyroscope provides this information with varying degrees of reliability and accuracy, so how does a fiber optic gyroscope differ from other gyroscopes?
2.Optical fiber technology
As the name suggests, fiber optic gyroscopes use fiber optics to perform their work. Fiber optics are made of glass and are used in many applications to transmit light from one point to another. Fiber optic cables are commonly used in telecommunications such as telephones and the Internet, and are extremely fast and reliable.
In a fiber optic gyroscope, this method of light transmission is not used to transmit information elsewhere, but is tightly wound in an independent closed loop within the gyroscope. This allows the fiber optic gyroscope to take advantage of the "Sagnac effect."
3.Sagnac effect
This phenomenon, discovered by French physicist Georges Sagnac, is at the heart of how every fiber optic gyroscope works.
Inside the gyroscope, the laser is used to send two separate beams of light through an optical fiber. Each beam travels in the opposite direction, propagating the entire length of the fiber, up to 5 kilometers. Each beam then returns to the light detector, recording its travel time.
Take an international flight at cruising altitude. The aircraft is stable, flying straight, level, with no rotation changes.
When there is no rotation change in the aircraft, the beam returns to the detector at the same time. In this case, there is no delay or "phase shift" between each beam. The aircraft was detected as stable and did not undergo any rotation rate around any given axis.
However, when the plane turns, Sagnac will come into full play. When the aircraft turns to the right, the fiber optic gyroscope dedicated to the rolling shaft will experience an arrival delay between the two beams. As it rotates, the distance each beam must travel changes.
When the detector is slightly closer to the traveling beam, the light traveling against the direction of rotation will return first. In this example, the beam propagating to the left will return first. Similarly, a beam traveling to the right will take longer. The phase shift between each beam is detected as a rotational change. This critical information can then be sent downstream to an aircraft, spacecraft, submarine or missile to stabilize it. This happens at a rate of hundreds of times per second, providing very precise measurements.
4.Fiber optic gyroscope calibration
As with any gyroscope, error sources, deviations, and noise must be carefully considered and corrected. During manufacturing, fiber optic gyroscopes are calibrated to correct for several potential sources of error that can be introduced by the gyroscope itself or the environment. When calibrated, fiber optic gyroscopes provide a very high level of performance.
Why use fiber optic gyroscopes?
Fiber optic gyroscopes have become ubiquitous in many applications, with several attractive properties. They remain reliable in harsh environments with intense vibration, have no moving parts, strike a good balance between price and high performance, and can last a long run.
5.Summary
Ericco developed fiber optic gyroscope ER-FOG-851, ER-FOG-910, low cost, good performance, can be widely used in optical pod/flight control level, INS/IMU, platform stabilization device, positioning system, north finder, high precision measurement/navigation system and servo system, if you are interested in learning more, Please feel free to contact us.
HDD technology breakthrough! North seeker helps with orientation in trenchless construction
As the core technology of trenchless pipeline laying, HDD technology places extremely high demands on the direction control of the drill b...

-
With the advantages of all-solid state, high performance and flexible design, fiber optic gyroscope has become the mainstream inertial...
-
Horizontal directional drilling technology completes the task of laying underground pipelines without destroying the surface environment....
-
For more information, please indicate in the “Ask for a Quote” box at the bottom of the page that you learned about this North Finder fr...