The gyro theodolite is a high-precision precision directional instrument that integrates light, machinery and electricity and is widely used in mining, construction, surveying and mapping, military, aviation, aerospace and other fields. Because it is not limited by time and environment, observation is simple, convenient and efficient, and it can ensure high accuracy, so it is an advanced directional instrument. Compared with traditional geometric orientation, gyroscopic orientation has huge advantages; compared with GPS global positioning system, it is not subject to electromagnetic wave propagation conditions and still has many advantages. Especially in production mine measurement, it is currently the most advanced directional instrument. However, due to some limitations in the design of domestic gyro-theodolite, most of the gyro-theodolite in most production units and colleges and universities in my country have been damaged to varying degrees, which not only increases the repair cost sharply, but also seriously affects production, teaching and research. In view of this, the author conducted research on how to improve the service life of the gyro-theodolite based on the principle and use experience of the gyro-theodolite, and improved some circuits to provide specific methods to extend the service life of the gyro-theodolite.
1.The composition and working principle of the gyro-theodolite
1∙1 Composition of gyroscopic theodolite
The gyro-theodolite consists of a gyroscope, theodolite, and an inverter power supply. The functions of each part are as follows:
Theodolite: Determination of direction value during orientation;
Gyroscope: Determination of true north direction when orienting;
Inverter power supply: Convert 24V DC power into 36V, 400Hz, three-phase medium-frequency AC power through the inverter circuit to drive the gyro motor to rotate at high speed to achieve orientation.
1.2 Working principle
Suppose a gyro theodolite is set up on the earth's surface at a geographical latitude of , and point O is the intersection point between the gyro room and the suspension. With O as the origin, establish a coordinate system OXYZ fixed to the ground. The OX axis points horizontally to the north, and the OY axis points horizontally to the west. OXYZ rotates at the Earth's rotation angular speed of relative to the geocentric reference frame.At the same time, a moving coordinate system Oxyz fixedly connected to the gyro room is established at point O. The Ox axis is parallel to the main axis of the gyro. Looking in the forward direction counter to the Ox axis, the top rotates counterclockwise, and the angles are all counterclockwise. The meaning of angle is the deflection angle of the main axis relative to the meridian plane, the angle is the pitch angle of the axis relative to the horizontal plane, and the angle is the nutation angle of the gyro. The principle is shown in Figure 1.
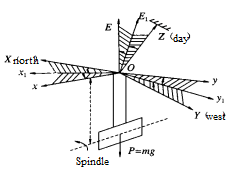
Figure 1 Principle of gyro-theodolite gyro motion
2.Factors that restrict the service life of gyro theodolite and methods to extend its service life
From the working principle of the gyro theodolite, it can be seen that in order to measure the true azimuth angle of a certain side of the mine, it is necessary to observe the gyro movement for a long time. The gyro motor works in a high-speed rotation state. Therefore, the factors that restrict the service life of the gyro should be studied from the following aspects. consider.
2∙1 Instrument factors
The instrument factors that affect the service life of gyroscopes are mainly analyzed from the two aspects of gyro motor and inverter power supply. At present, most of the hanging gyros are used, which are relatively representative gyros in the world. They have their own characteristics in specific structures. . But the overall structure is basically similar. The core component of the gyroscope is the gyro motor, which is installed in a sealed, hydrogen-filled gyro room and hung up through a suspension strap. Two guide wires, a suspension strap and a bypass structure are used to power the motor. Therefore its structure is very compact. What is particularly important is that the suspension belt must not only withstand the torque of the gyromotor when it rotates at high speed, but also the weight of the gyromotor, as well as the passage of strong current. The complexity of the process can be imagined, so if you are not careful during use, will cause it to be damaged.
2∙2 Observer quality
Gyroscope operators should be trained in advance. On the one hand, they should ideologically strengthen their subjective awareness of caring for the instrument; on the other hand, their professional quality should be improved, especially so that they have an accurate understanding of the principles of the gyroscope. In this way, the operator will consciously operate according to the operating procedures during the instrument observation process, thereby reducing man-made damage to the instrument.
2∙3 Observation environmental conditions
As mentioned before, when the gyroscope is working, the gyro motor rotates at high speed, generating a large precession torque. At the same time, the motor's guide wire and suspension carry strong current through it, and the power amplifier part of the inverter power supply works with high current. state, so high heat will be generated in the gyro room and inverter power supply, causing the gyro motor and inverter power supply to heat up. In addition, the operation process takes a long time, so in high temperature weather and direct sunlight, the instrument is easy to burn and shorten the instrument. life.
It can be seen from the above analysis that the service life of the gyrotheodolite is restricted by many factors. If a certain link is not paid attention to properly, the instrument will be damaged. Therefore, operating the instrument reasonably and carefully and improving the efficiency of the inverter power supply are the keys to extending the service life of the gyro-theodolite. Based on many years of use experience, the author conducted corresponding theoretical analysis and research, and came up with the following specific methods to extend the service life of the gyro-theodolite:
(1) Operate the gyro-theodolite strictly in accordance with the operating procedures, which is the basis for ensuring that the gyro-theodolite is protected from accidental damage. The following points should be noted:
- The instrument must be used by personnel with certain operating experience who are familiar with the performance of the gyro-theodolite.
- Before starting the gyro motor to reach the rated speed and during the process of braking the gyro motor. The sensitive part of the gyro must be in a locked state to prevent damage to the suspension guide wire.
- When the sensitive part of the gyro is in a locked state and the motor is rotating at high speed, it is strictly forbidden to move or rotate the instrument horizontally, otherwise a large torsional force will be generated, compressing the bearings and damaging the instrument.
- Before turning on the gyro inverter power supply, check the connections repeatedly. When using an external power supply, pay attention to whether the voltage polarity is correct. Do not turn on the inverter when there is no load.
- When storing the gyroscope, put it in the instrument box and add desiccant. The instrument should be stored correctly and not placed upside down or lying down.
- When carrying out long-distance transportation, special shock-proof packaging boxes should be used.
- During summer or sunny weather observations, try to avoid direct sunlight on the instrument.
(2)Improve the high current and high voltage circuit part of the inverter power supply (the power supply circuit is shown in Figure 2).
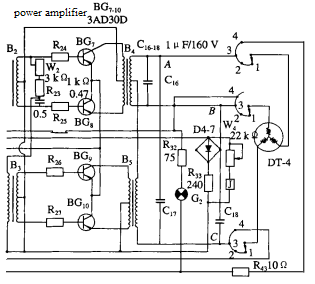
Figure 2 Gyro inverter power supply circuit
The cadmium-nickel battery of the inverter power supply is also an important factor that restricts the service life of the power supply. Nickel-cadmium batteries have a strict memory effect. In order to eliminate the memory effect, the author recommends using nickel-metal hydride batteries to replace nickel-cadmium batteries or installing a protection device on the gyro-theodolite discharger. To this end, the author designed a protection circuit for reference by each unit. The circuit is shown in Figure 3.
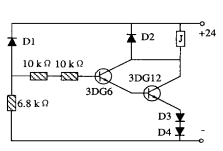
Figure 3 Principle of gyro discharger
Summarize
The above gives specific methods to extend the service life of the gyro-theodolite. Judging from the actual application results of this unit, it not only extends the
The service life of ERICCO can ensure the yield rate of experiments and save a lot of instrument repair costs. ERICCO's gyro theodolite includes ER-GT-03 Quick Gyro Theodolite, ER-GT-05 Low Temperature Gyro Theodolite, and ER- GT-20 Portable Gyro Theodolite. They can be used in tunnel penetration measurement, subway engineering measurement, mine penetration measurement, and navigation equipment calibration. Our company has strict requirements for the preservation and use of gyro theodolite.
If you want to purchase a gyro-theodolite, please contact our relevant technical staff.